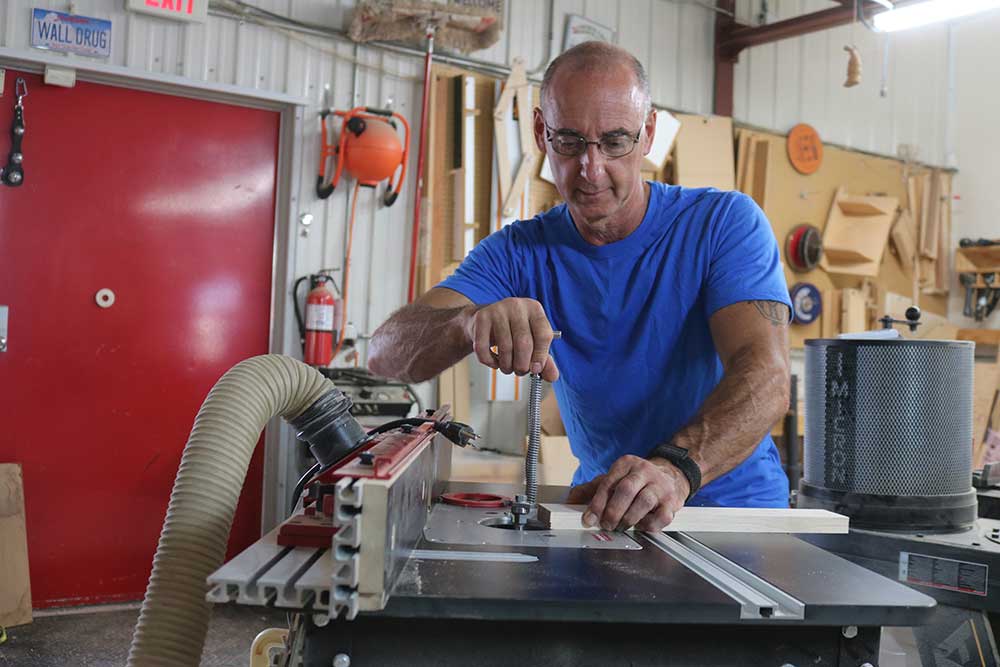
How to Trim Edge Bands
George VondriskaMaster woodworker George Vondriska shows you how to avoid sanding through the veneers on your woodworking projects by using a router to trim edge bands. A WoodWorkers Guild of America (WWGOA) original video.
When you've got banding applied to sheet goods, like I do here, and it's leftover size, you've gotta get that trimmed down. Now, one way to do it would be to get on here with a sander and start working on that banding. What concerns me with that is that, it's too easy to get a sand-through on the veneer here. Remember that veneers are just getting thinner and thinner all the time. So, if I get a sand-through, I'm going to be in trouble.
The core of this is showing through. Instead, I'm gonna use a router. Now, let me talk about the router setup. It's really very simple. I've got a three-quarter inch straight bit in the router.
I've got a half inch MDF piece, which is bolted right to the bottom of the router. With a little recess in here that the bit can nest inside. The way this is gonna work is that, the MDF is gonna sit on the material. The bit is gonna be able to cantilever past the sheet goods, trim the banding, registering it, referencing it right down to the level of the sheet goods. So, what's critical with this is that, I need to get the height of the cutter set, so that the bottom of the cutter is even with the material.
I gotta make sure that's right before I start doing any cutting. Otherwise, instead of sanding-through I'm gonna have a cut-through on this veneer, if I cut too deeply. So let me get rid of this. Bring out a piece of scrap. The reason the paper is here is cause, I found that that's a pretty good way to get this whole process started.
Loosen up my router, of course, it's unplugged. I'm gonna raise it. So right now, that router bit isn't even close to touching the material. As I lower the cutter, I'm gonna use this paper as a feeler gage. I'm sliding it in past the bottom of the bit as I lower the bit.
And what's gonna happen as I drop it is, it's gonna get to a point where it catches. The tip of the cutter catches on the paper. Right there. I'm gonna back up just a little bit. Standard paper is about .003 of an inch thick.
So, if I did this right, that's leaving the tip of my cutter about .003 above the material. I'm gonna hold this down, turn that by hand. And what I'm feeling for is, are the cutter tips dragging at all on the surface of the material. They're not, but I want to make a test first. So, I'll plug this in and I'll just do a little test cut right here on this piece of scrap, see if I'm digging into it at all.
If I'm not, we'll try the real deal. What the test on the scrap tells you is, if you're set too deep and gonna take too much away, cause I know it'd cut into the surface. What it doesn't tell you is, if you're set just a little bit too short, as I cut into the banding here on this piece, I'm still a little bit higher than I wanna be. So, I'm gonna increase my depth to cut, do another test cut. Then we'll come back, finish this off once the depth is perfect.
Once this depth is cut, that does a beautiful job of skinning that down. It's left that banding just a, jeez, a gazillionth of an inch above the face with just a little bit of finish sanding, it's gonna knock it right down perfect. And the cut quality off the router, but it's really good. So, very little work to finish this. I'm ready to flip this over, do the trimming on the other side and that piece is gonna be all done.
i was thing he was going to use a flush trim bit, but i love to know more than one way to skin a cat (wood).
I made the jig and it works just as described as long as the edge bands are not on all 4 sides. I make a lot of decorative cutting boards and like to attach the edge bands on all sides; then proceed to trim the edge bands. I think I will need to do just 2 sides and use the jig and then glue the other 2 sides and use the jig for them. LMK if I am missing something. Thank you. Wilson
Why not just use a flush trim bit?